Direct lithium extraction processes are the engineering solution to add more value and extract more Lithium Carbonate equivalent from mining ventures especially in South America. The technology is focused on brines. Check out an overview of lithium for batteries
- Reduction in cost
- Faster process
- Modular and therefore scalable.
- Improvement in quantity of LiCO3 or LiOH recovered
- Reduction in carbon needed
Methods of DLE
There are 3 primary technologies for DLE in brine.
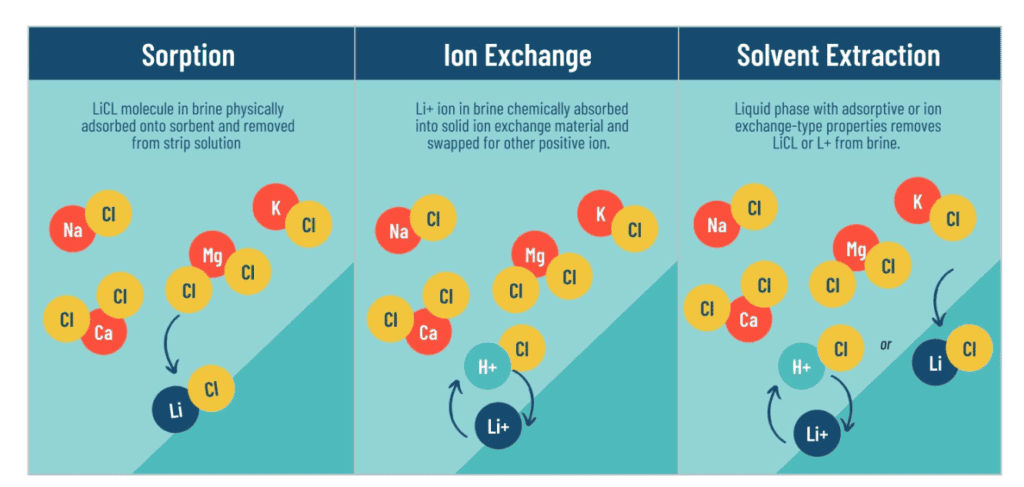
Companies using direct lithium extraction technologies
There are multiple technologies and the race is on to find the most effective.
Vulcan Presentation
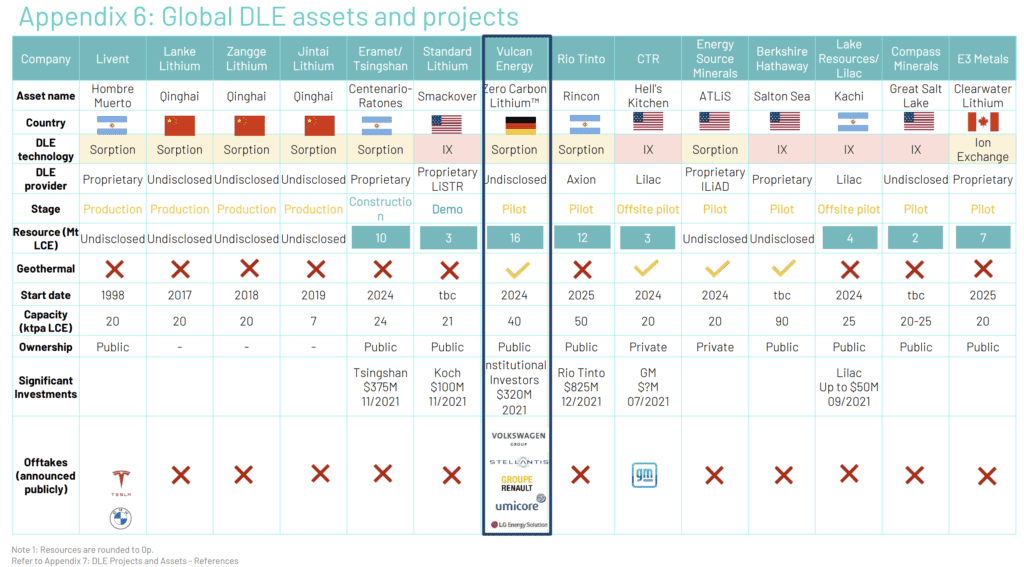
Anson Resources Comparison
A comparison provided by Anson Resources in 2023 is a year later than above
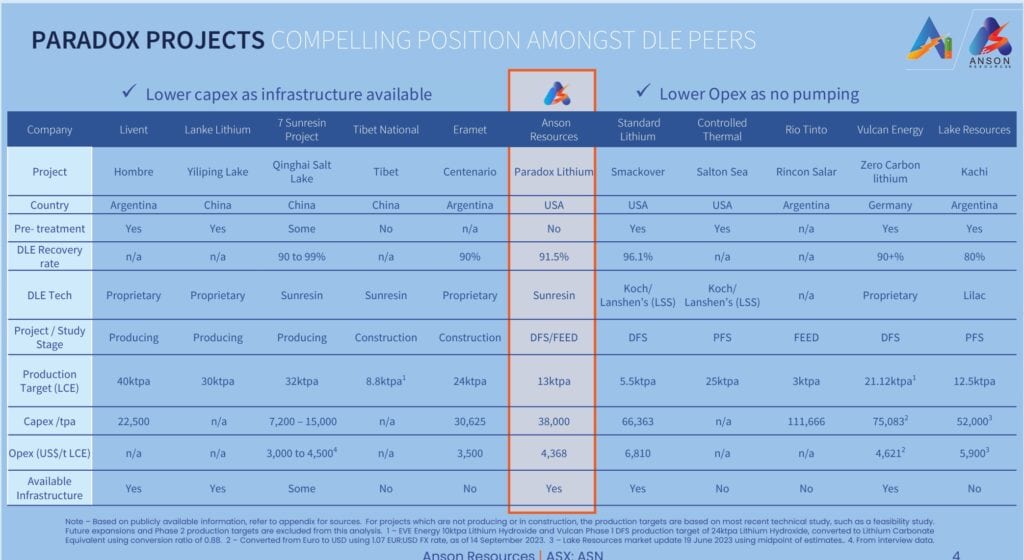
Some companies including Anson are not listed in the table above.
Salton Sea vs Rhine Valley Brine
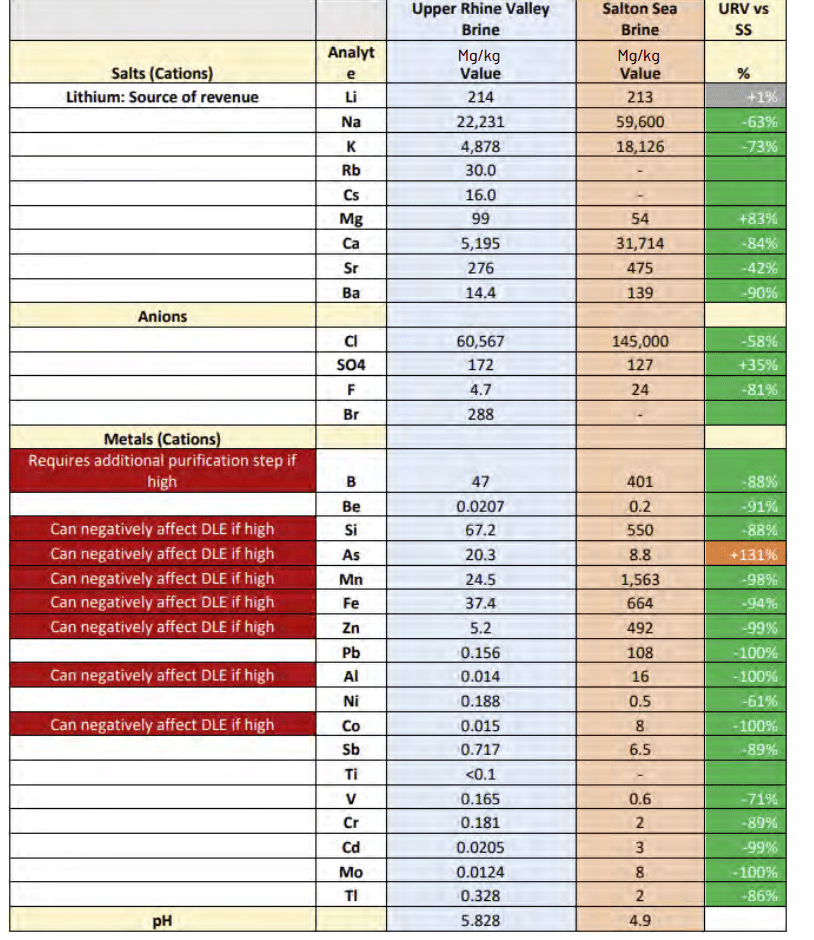
Other DLE Miner Technology
Anson Resources (ASN.ASX) reported in June 6 2022, that they had achieved higher lithium recoveries achieved from their test work at Paradox Project in Utah USA. Had 91.5% recoveries against previously estimated 80% They also intend to pull bromine out of the brine in anticipation of Zinc bromate batteries coming online in mid 2020’s
Anson is partnering with Sunresin’s DLE technology to provide good ESG, operational and economic advantages in producing lithium carbonate at the Paradox Project, including:
- Lithium DLE estimated recovery of 91.5% (against 80% from 2 other un named suppliers) (refer ASX announcement 13 August 2021). (ASX Announcements).
- No requirement for pre-treatment
- Use of water (organic process) rather than chemicals to wash the lithium from resin
- Longest recovery lifespan of bulk industry-grade lithium extracting resin to maximise the unit cost of production for the DLE process.
Vulcan Schemematic – geothermal energy plant. With the brine after using the energy for geothermal power then extract lithium and then finally reinjection of brine back into the ground.
Existing Direct Lithium Extraction Projects
Jade Cove Investments in 2020 have a good breakdown of existing projects. All are brownfield sites. DLE cannot be “copied and pasted” and needs to be project based. Some are hight in Mg and SO4, others are high Mg brine. Many use evaporative as well, to concentrate first.
Project | Started | Tonnes LCE | Owner | Location | Notes |
---|---|---|---|---|---|
Fénix Project | 1998 | 20,000 | Minera del Altiplano S.A. (Livent Corporation), | Minera del Altiplano S.A. (Livent Corporation), | Some DLE then shipped to lower altitude. |
Lanke Lithium | 2017 | 15,000 | Qinghai Salt Lake Industry Co. Ltd. | Qinghai, China | Russian technology. |
Zangge Lithium Carbonate Project | 2019 | 10,000 | Zangge Potash Fertilizer Co. Ltd | Qinghai, China | Ramping to 20,000T |
Minmetals Yi Li Ping Salt Lake Project | 2020 | 1,000 | China Minmetals Corp. | Qinghai, China | hybrid evaporation & membrane-type process to separate LiCl and MgCl2 |
Jintai Lithium Carbonate Project | 2019 | 7,000 | Qinghai Jintai Potash Co. Ltd. | Qinghai, China | Mg brine. |
Project Altis | 2022 | 20,000 | Energy Source Minerals | Salton Sea, CA USA | Into production Q4/2022 |
Kachi | 2023 | 10,000 | Lake Resources | Catamarca Province | Pilot phase, 100,00 by 2030 |
Rhine Valley | 2022 | 5,0000 | Vulcan Resources | Upper Rhine Valley, Germany | combined geothermal with DLE for zero cargon |
Issues with DLE – Water Use
Adsorption is the only commercially proven approach to DLE. The lithium molecules in the brine adhere to an adsorbent substance, removing them from surrounding impurities. Then you need to strip the lithium from the adsorbents and that requires a lot of fresh water, a big problem if the brine resources are in arid areas. There will be solutions such as desalination, but that will add cost and energy.
- Livent uses 71.4 metric tons of fresh water per tonne of LCE
- Lilac reported in pilot testing it uses between 10 and 20t
- EnergyX says it uses less than 20t.
Summit Nanotechnology
A private startup company Summit Nanotechnology from Canada has their nanotechnology DLE in 6 mines in South America (Chile and Argentina) for Lithium Carbonate Li2CO3 and a clay based NaOH in USA. Cleantechnica interviewed the Summit CEO Amanda Hall in March 2023.
Project ATLiS

Improving Lithium Extraction from Spodumene
Lithium from hard rock spodumene is concentrated from 1.5% in rock, to 6% Lithium, then usually sent to China for refining. Pilbara Minerals has announced some refining improvements. Many of these come from water treatment technologies or other treatment systems. Calix Limited is in the processing industry, and so expect to see more technology to improve Li production from other companies.
- Calix Limited’s (ASX:CXL) flash calcination technology test-work concentrates it with high calcination conversion rates (>95% for alpha to beta spodumene phase transformation) using fine flotation spodumene concentrate.
- The contained lithia content of the product is expected to increase from ~5.7-6.0% in spodumene concentrates to >36% in lithium phosphate salts, thereby optimising offshore product logistics, reducing associated carbon emissions, and minimising waste in the destination market.
SunResin Direct Lithium Extraction Technology
Name | Tonnes | Production |
---|---|---|
Operating Projects | ||
Zangge Lithium | 10,000 | LiCO3 |
Qinghai Jintai Lithium | 3,000 | LiCO3 |
Minmetals | 2,000 | LiCO3 |
Minmetals Phase 2 | 4,000 | LiCO3 |
Projects Under Construction | ||
Qinghai Salt Lake BYD Resources pilot | 600 | LiCO3 |
EveBattery | 10,000 | LiCO3 |
Qinghai Chaidamu Xinghua Lithium | 5,000 | LiCO3 |
Tibet Summit (Argentina) | 25,000 | LiCO3 |
Projects Under Contract | ||
Tibet National Energy | 10,000 | LiCO3 |
Qinghai Jintai Lithium | 4,000 | LiOH |
Anson Resources (phase 1 2024) + bromine | 10,000 | LiCO3 |
Further Reading
Direct Lithium Extraction—A 21st Century Dot-Com Boom or Bust? (spe.org) Journal of Petroleum Technology May 2022 They mention that 2021, DOE identified 15 teams of university researchers as semifinalists in Phase 1 of the competition and awarded $40,000 grants to each team, which then advanced into Phase 2.
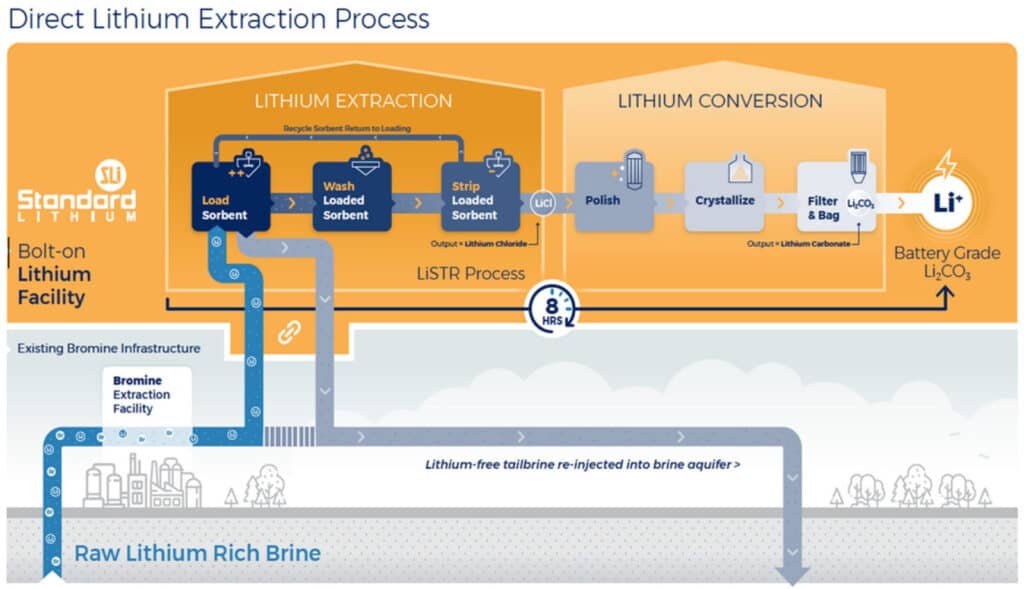
The Standard Lithium “LiSTR” proprietary process uses a solid ceramic adsorbent material with a crystal lattice that is capable of selectively pulling lithium ions from the Smackover brine. The ceramic adsorbent materials are mounted in stirred-tank reactors that contain the tail brine. In the second step, the adsorbent releases the lithium for recovery. The brine is at 700C. The project is 4.3mT of LCE, with annual production at 20kT LCE
Technical Review
Lithium Recovery from Brines Including Seawater, Salt Lake Brine, Underground Water and Geothermal Water by Samadiy Murodjon, Xiaoping Yu, Mingli Li, Ji Duo and Tianlong Deng 2020 Open Access paper here is a detailed view.