CATL has just announced the introduction of their new battery called Qilin which means there are top 2 ev batteries globally. CATL claim 1000 km with the new Qilin technology with fast charging in 10 minutes . Mainstream ternary batteries supplied by China’s top battery maker Contemporary Amperex Technology (CATL) currently have an energy density of 160Wh/kg, with the highest level of 180 Wh/kg. The energy density of ternary batteries produced by BYD stands mostly at 160Wh/kg, while the highest level is 161Wh/kg. Batteries are key to a rapid increase in the production for EV cars globally
A detailed press release is found on CATL website https://www.catl.com/en/news/958.html
Qilin will boost its volume utilisation rate to 72%, the world’s highest, versus 50% for its first-generation launched in 2019, the firm said, and increase the battery system’s energy density to 255 Wh/kg. (Reuters). CATL and Tesla have a close working relationship and CATL currently supplies many of Tesla Model Y and Model 3 batteries.
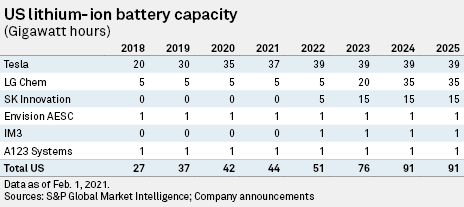
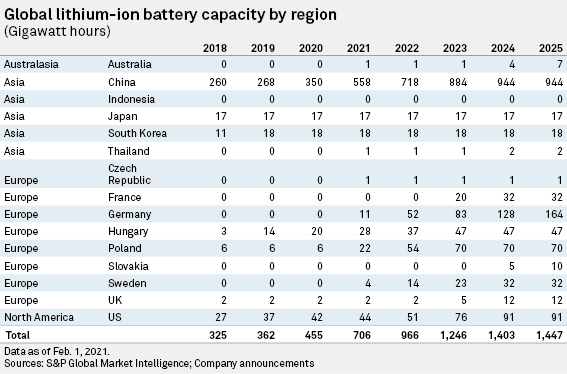
CATL produced 41.5 GWh of batteries in the first four months of 2022
Tesla Stats
Tesla announced their 4680 at Battery Day in Sept 2020, and is ramping up production of its 4680 batteries at Texas but ramp up is been slower than desired.
End of Solid State?
With the shortage of battery supply both will dominate over the next few years, and it may be that solid state batteries cannot compete if these have addressed energy density, safety, fast charging, and thermal efficiency.
Top 2 EV Batteries Globally Compared
Tesla 4680 Battery
The new top 2 ev batteries potentially globally will be the Tesla 4680 and the Qilin, promised in 2023.
About 1m 4680 had been produced by Tesla by the start of 2022, and by June 2022 estimated at 1m per month but will need to scale to 20 m per month to meet demand from cars, cybertruck and semi product lines. Tesla has used the 4680 to modify their vehicle production system. Will other manufacturers?
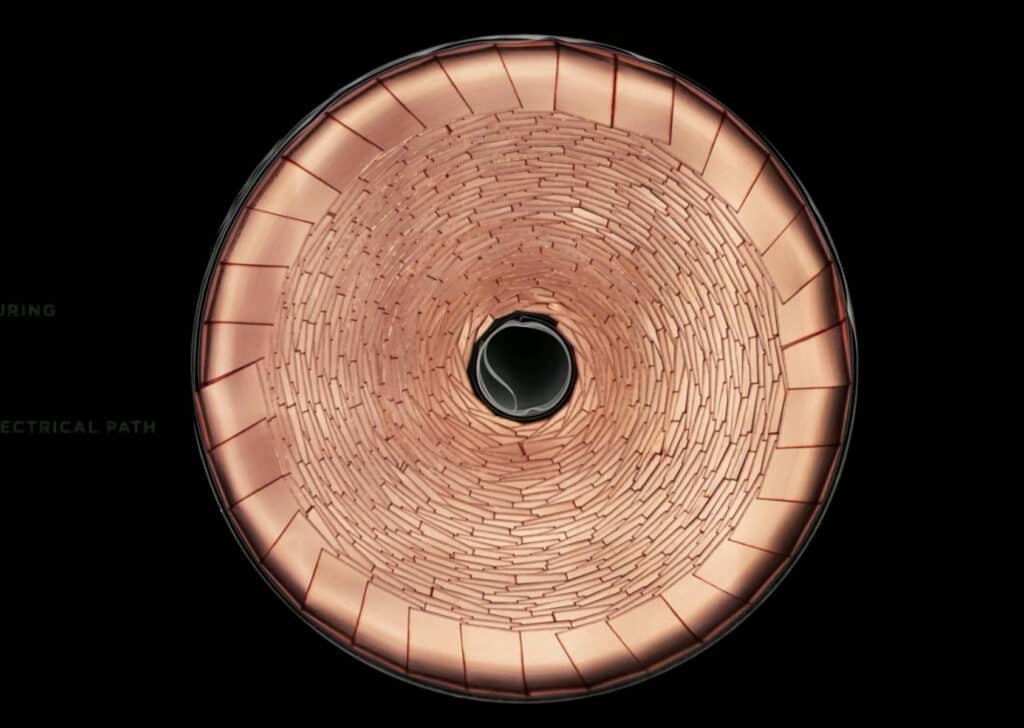
Qilin Battery
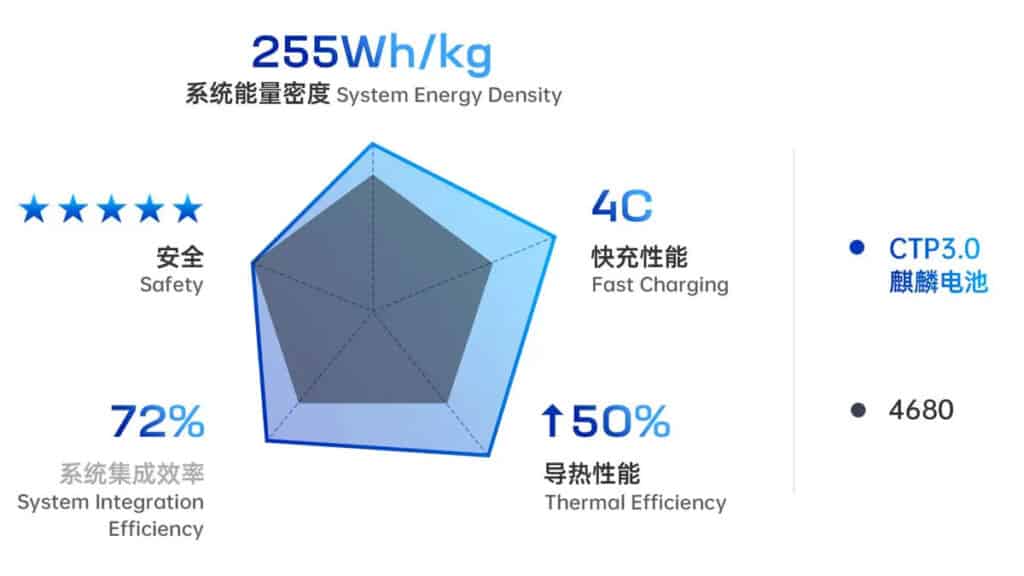
The Qilin battery is supported by the following
- Improved cooling system – quadruples the cooling efficiency
- Structural cell to pack
- The lithium quaternary with is the pack level 255 Wh/kg at the pack level
- The LFP version comes in at 160 Wh/kg but is much cheaper and will probably dominate.
That means that LFP will completely change the need for solid state batteries.
Mainstream ternary batteries supplied by China’s top battery maker Contemporary Amperex Technology (CATL) currently have an energy density of 160Wh/kg, with the highest level of 180 Wh/kg. The energy density of ternary batteries produced by BYD stands mostly at 160Wh/kg, while the highest level is 161Wh/kg. .
Currently, these batteries come to 125 Wh/kg. If Tesla were to actually install the CtP battery with the 160 Wh/kg mentioned, the energy density would increase by 28 per cent (electrive.com)
Competitive Battery Manufacturers
A competitor, Guoxuan Hi-Tech mainly produces LFP batteries while CATL and BYD both make ternary and LFP batteries. In 2019, the installed capacity of LFP batteries produced by Guoxuan Hi-Tech stood at 3.2GWh, with a market share of 15.1%, with the share of ternary batteries at only 0.5%.
Tesla Production Target
Tesla’s target is 10 GWh [annualized] production capacity initially but increasing to be in the order of 200 GWh or more. Tesla’s goal is
- 14% improvement in cost/kWh coming from the change in cell form factor.
- 18% improvement in cost/kWh as a result of the 10× manufacturing footprint reduction and 10× manufacturing energy consumption reduction.
- The new dry manufacturing process enables pressing the active battery powder material directly into a film. The new manufacturing process is based on Maxwell Technologies’ proprietary “proof of concept” process.
- 5% improvement in cost/kWh coming from the increased utilization of silicon in the battery cells.
- 12% reduction in cost/kWh coming from improvements in the cathode material.
- 7% improvement in battery pack cost per kWh as a result of Tesla’s new integrated vehicle design.
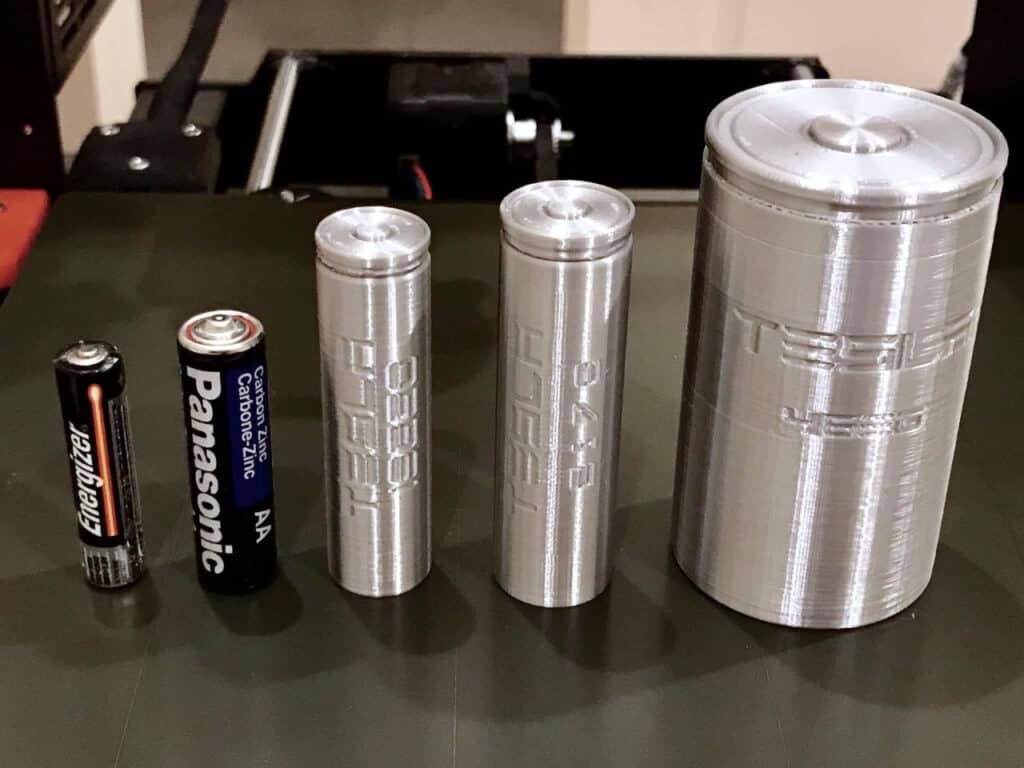