Three years ago at the Tesla Battery Day Elon Musk announced the Tesla 4680 battery ramp, following the purchase of Maxwell Technolgies. They had developed a “dry/semi-dry” electrode cell manufacturing process. The format of the battery (46mm diameter, 80mm height) was a transformation change from the connectors being at end of the roll of cathode and anode to all alone the length. Key advantage was the distance the current flowed. Simple as it sounds in hindsight, Tesla said it would lead to the following benefits.
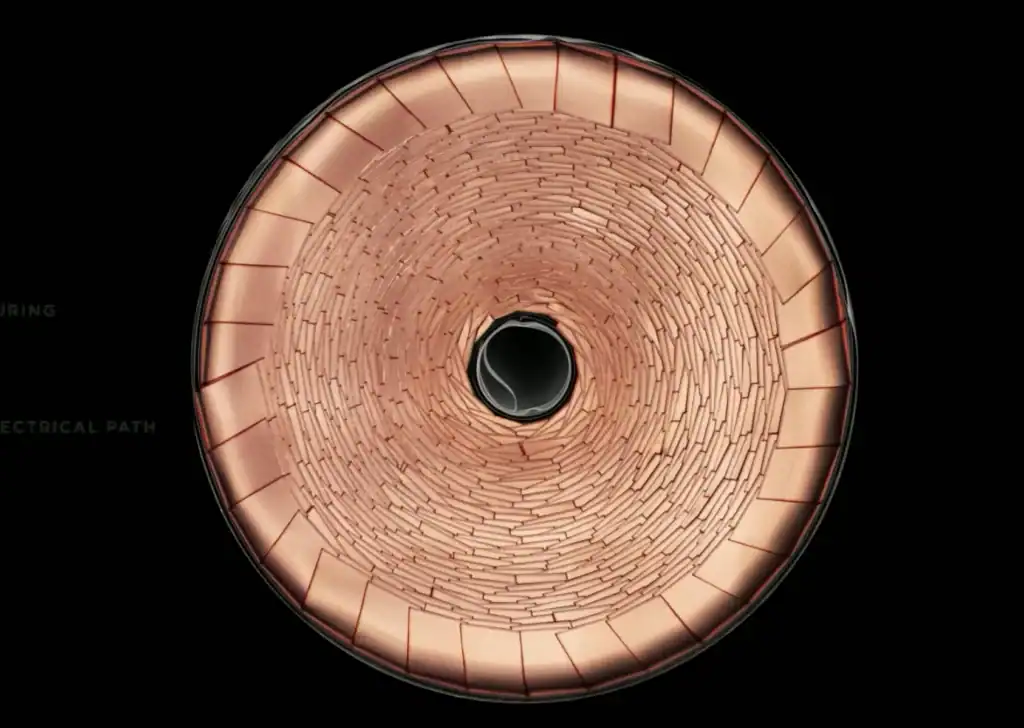
Maxwell was not the only company Tesla acquired for some of the patents or products for new battery improvements. SiILion, Inc was acquired in 2021 for silicon anode and Tesla has an offtake agreement with Magnis Energy Technologies for anode active materials AAM graphite and USA production.
Aggressive Tesla 4680 Battery Ramp
- January 2022: 1M 4680 cell produced
- January 2022 ~ June 2023 (17 months): 9M additional 4680 cells produced (10M total)
- June 2023 ~ October 2023 (4 months): 10M additional 4680 cells produced (20M total)
- January 2022: 1M 4680 cell produced
- January 2022 ~ June 2023 (17 months): 9M additional 4680 cells produced (10M total)
- June 2023 ~ October 2023 (4 months): 10M additional 4680 cells produced (20M total)
- 20m on Oct 11 2023, Texas only batteries
- 95GWh
- Note that the cells from 2022 were mostly from Kato Road in California, and the 20 million was from the Texas Gigafactory.
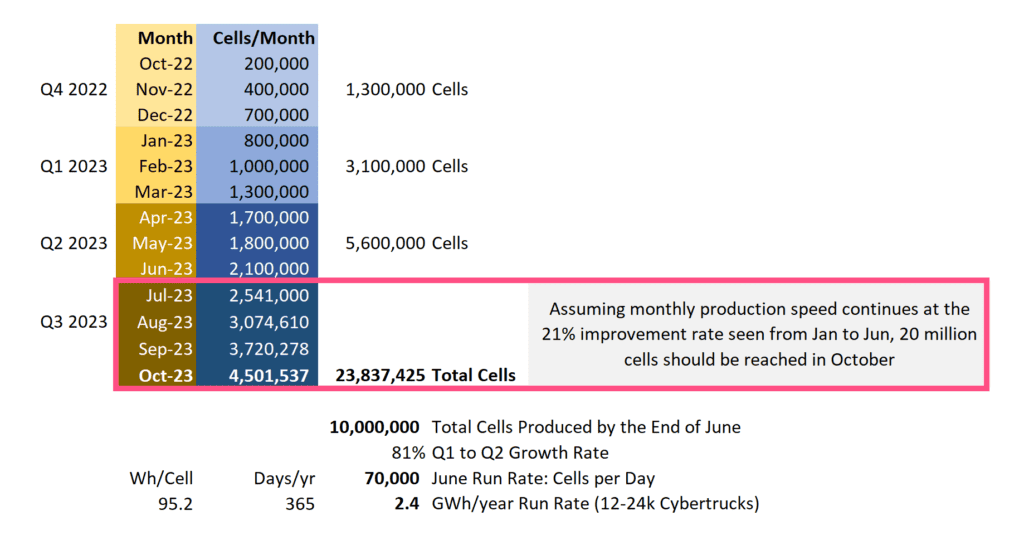
What Does it Mean for CyberTruck
Production | GWh | CyberTrucks |
---|---|---|
10m battery cells Both CA and TX | 0.95GWh | 7,310 |
20m battery cells Oct 11th, Texas only | 1.9GWh 10% more then Gen 1 cells | 14,620 based on 130 MW battery pack 1368 cells per pack |
In just under 2 years Tesla ramped up from producing their 1 millionth cell to their 20 millionth, while doubling the 10M cells produced to 20M in just 4 months that previously took 17 months.
If this isn’t what you call the definition of exponential growth, what is?
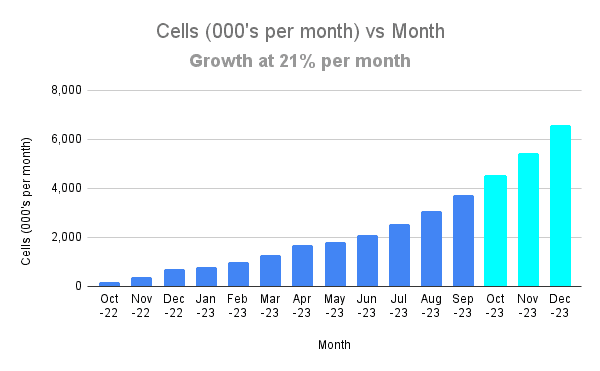
21% Growth
Production has increased by 21% YOY. With the next generation of 4680 batteries, the manufacturing can be multiplied by replicating the manufacturing process line. Panasonic is running a pilot 4680 production line at its Wakayama factory in Japan, and plans to start volume production later in the fiscal year that ends in March 2024. Others include LG New Energy, Samsung SDI, Envision Power, EVE Lithium Energy, CATL. With Tesla taking the lead in expanding production in the battery field in 2023, this has once again aroused the market’s high attention to 4680 battery. The top 10 4680 battery manufacturers in the world can be found at https://www.takomabattery.com/top-10-4680-battery-manufacturers-in-the-world/.
What Does This Production Ramp Mean for Electric Vehicles?
The Limiting Factor says that as per his analysis from the Q2 earnings call they are
- Increasing the 4680 line speed in Texas by about 21% per month.
- Equates to about a 5.13 GWh/yr run rate, which is about 20-30% more than a typical battery line
- The lines at Austin are capable of 20-25GWh/line. With 4 battery lines for a total of 100GW per year
- So even though ~5GWh is a lot of cells, there is room to improve
- 5.13GWh is based on an assumption of 4.5 million cells per month at ~95 Wh/cell
- 95Wh/cell includes the 10% energy density increase Drew mentioned in the last earnings call.
- A ~5GWh run rate, or 4.5 million cells per month, is more than enough to ramp the Cybertruck.
- Depending on pack size, that could support a run rate of 25-50k Cybertrucks per year per line.
More Information
For the full battery day – check out this YT video
Tesla Video of Megapack Gigafactory at Kato Rd, Californian
Multiple Enhancements Increase Battery Performance
Research around the globe increases energy density (and corresponding weight), cycles, and manufacturability. Each of these may only add 5%, but in total add up to a learning curve of over 20% per year.
Top 10 4680 Battery Manufacturers
Company | Location | When | Quantity | Website |
---|---|---|---|---|
Tesla | Ca, Texas, Berin, NV | 2022 | Target is 3TWh by 2030 | https://tesla.com |
Panasonic | Japan | 2023 | Issuse with production have pushed to 2024 | http://holdings.panasonic/global |
LG New Solution | South Korea | 2023 | Investing in new factory | https://www.lgensol.com/en/ |
Samsung SDI | South Korea | 20224 | 10GWh 4680, 4695 and 46120 | https://www.samsungsdi.com/ |
EVE | China | 2023 | 4695 in Dec 2022. Energy density of 350Wh/kg, reduce manufacturing cost 50% | www.evebattery.com |
BAK | Shenzhen China | 2024 | Began 2019, prototype 03/2021, heights 70 to 160mm 280Wh-330wh/kg | www.bakpower.com |
Envision Power | South Carolina | 2024 | New factory for BMW, 30/GWh factory | http://www.envision-group.com |
CATL | China | 2024 /2025 | Planned 8 lines, 12GWh, now 20GWh by 2025 | www.catl.com |
SVolt | Great Wall China | 2024/2025 | First 23Ah 4680 shown in 2021, 235Wh/kg, 1200 cycle | http://www.svolt.cn |
Lishen | China | 2023 | 500 million Ah, preproduction samples | http://www.lishen.com.cn |
Hundreds of Improvements
CleanTechnica reported after Battery Day, Tesla rolled out hundreds if not thousands of small improvements that bring step change improvements to the fundamental building block of Tesla’s business — the battery cell.
Factor | % Increase | Implication |
---|---|---|
Change in form factor | 14% | Bigger cell |
Manufacturing footprint and energy | 18% | The new dry manufacturing process enables pressing the active battery powder material directly into a film. The new manufacturing process is based on Maxwell Technologies’ proprietary “proof of concept” process. Process is not at production scale yet, but there is a “clear path” to large scale production. |
Silicon | 5% | Increase from silicon in anode (increase in cycles, density) |
Cathode | 12% | improvements in the cathode material. |
Vehicle design & structural battery pack | 7% | Tesla redesigned its vehicles using new front and rear castings that integrate with the battery pack. To accomplish this, Tesla developed a completely new alloy to enable casting of some of the largest components in the automotive space. These bolt directly into a new “structural battery,” eliminating the need for redundant, parallel elements in Teslas. |
Total | 56% | Improvement is in Generation 1, and now in generation 2, and Generation 3 i design at Kato Rd factory |
All told, Tesla’s redesign of the battery, cathode, and vehicle frame translates to an expected improvement of 56% in Tesla’s cost per kWh
Tesla in shareholder and quarterly meetings state they have achieved additional improvements for ver 2.0